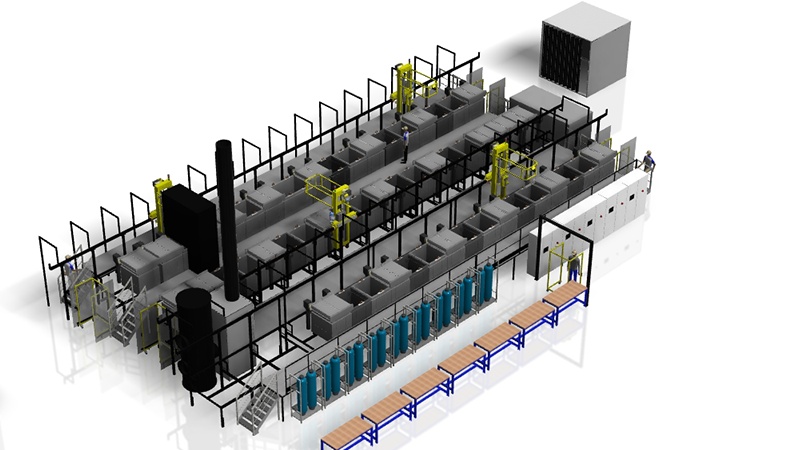
Our design office supports you on all of your surface treatment installation projects. From the feasibility study, to the turnkey installation, our engineers put their skills and experience at your service to design innovative installations and equipment. Our human-sized structure allows us to stay close to our customers.
- Detailed engineering and process control
- Mechanical, hydraulic, aeronautical, electrical studies, structural calculation
- Writing of technical files and maintenance booklets
- Research and development of new products
- Training file
- IT management supervision
At the very heart of our activity, the realization of surface treatment, penetrant testing and liquid and gaseous effluent treatment is our specialty. We put our know-how at your service for the design, construction and integration of your facilities to help you reach the targeted technical performance level while respecting your budget and applicable regulations.
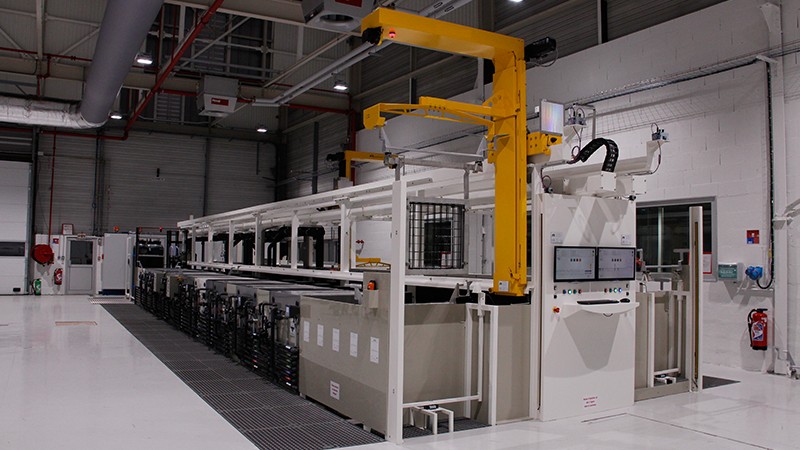
Chemical treatments
- Phosphatation in a bath or barrel
- Chlorinated or non-chlorinated degreasing
- Stainless steel pickling (range without nitric)
- Brightening
- Burnishing
- Non-destructive checks
Atmospheric treatments
- Fans
- Collector networks
- Gas scrubbers
- Deviseculeur
Water treatment
- Detoxification station and physicochemical neutralization
- Vacuum evaporation
- Sludge treatment
Printed circuit treatments
- Preparation
- Activation
- Copper pulsed current reinforcements
- Finishes
Aeronautical treatments
- Light alloy anodizing treatments (OAC, OAS, OAD, TSA)
- Passivations / Conversions without Chrome IV
- Non Destructive Testing (NDT)
- Electrostatic or liquid penetrant – Nital
- Treatments Nickel Chemical, Hard Chrome, Cadmium
- Stainless steel / Titanium stripping
- Ultrasonic washing degreasing
- Solvent Degreasing – Vacuum Technology
- NADCAP processes
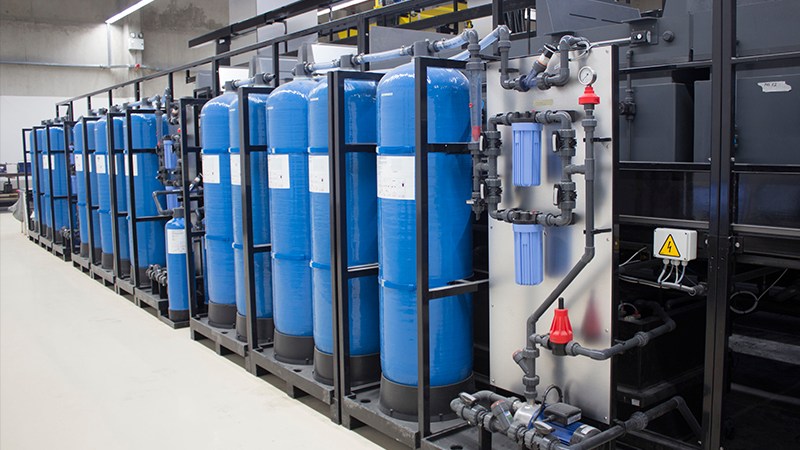
Electrolytic treatments in a bath or barrel
- Deposits of Zinc, Nickel, Chrome, Tin, Gold, Silver
- Allied deposits
- Chromic / Sulfuric Anodic Oxidation
- Electrolytic pickling
- Polishing / Brillantage
- Electrolytic coloring
- Rhodium
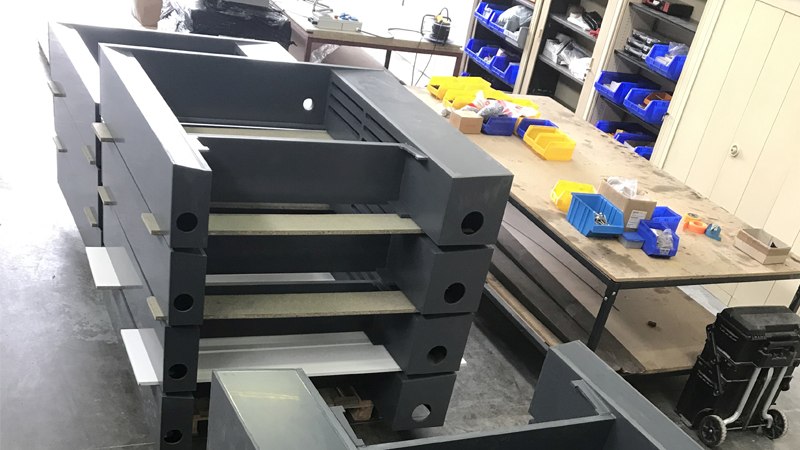
For all industrial needs for which, materials such as metal are not suitable, plastic sheet metal makes it possible to compensate for this lack and provides parts resistant to corrosive products. With this welding technique, custom parts can be created and thus meet the most specific needs.
- Boilerwork
- Machining and assembly of simple and complex custom parts
- In all thermoplastics: PVC, PE, PP, PPs, PMMA, PC, PETG, PA, PE-EL, PVDF.
- Machine protection (hood, casing, bell, etc.)
- Ventilation parts (hood, suction sensor, ventilation duct, etc.)
- Plastic furniture (bench, supports, sink, etc.)
- Technical parts (filtration box, gas washing column, paint booth…)
Our customers call on our teams for preventive and curative maintenance interventions. Involved in the manufacturing, assembly and commissioning phases, our technicians also train customer teams in the use and maintainability of their facilities. Electricians, automation engineers, boilermakers, site managers … They make customer satisfaction their priority.
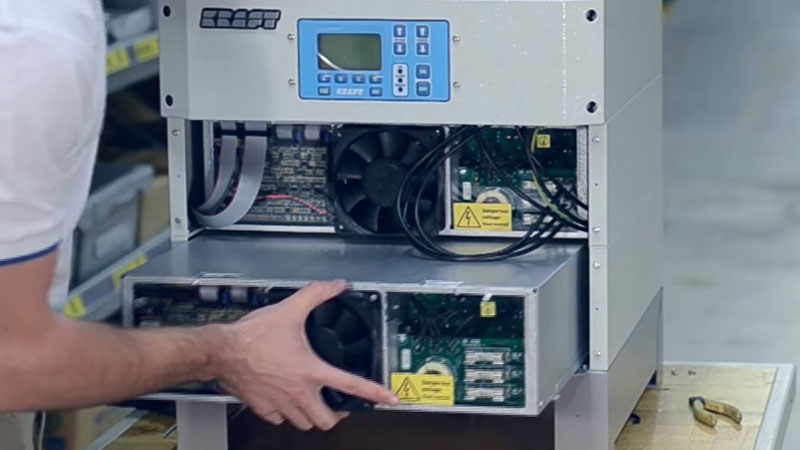
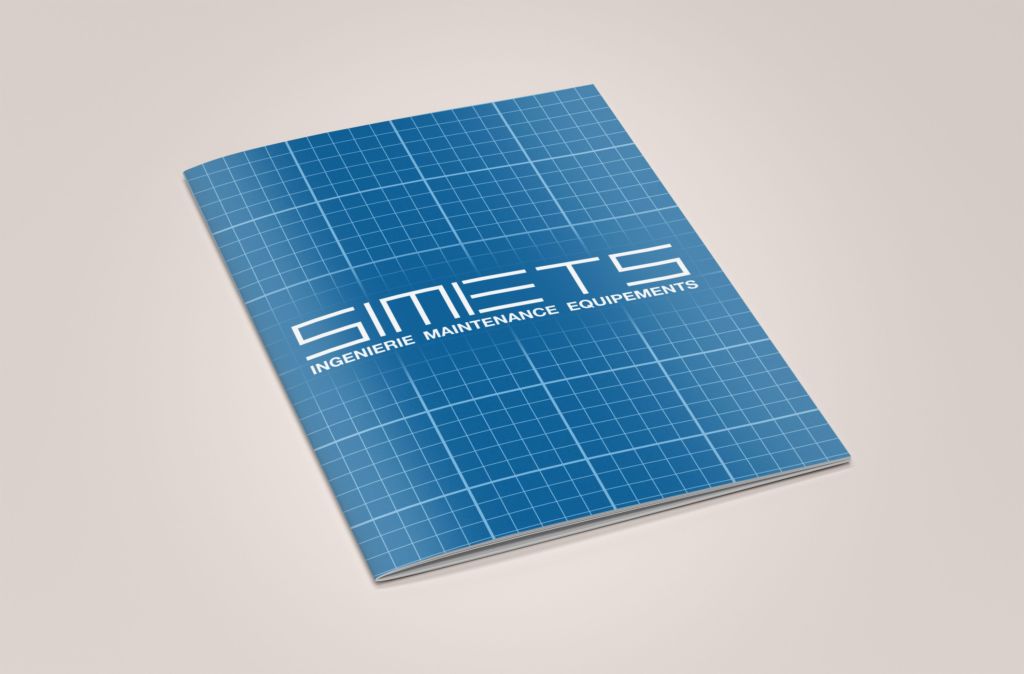
Organizing tailor-made, flexible and scalable training courses so as not to simply train our customers but to make them evolve sustainably by adapting to their priorities and their particular constraints is our objective. The training courses we offer are designed to meet the needs and expectations specific to surface treatment activities.
Training organization approved by the state, we offer a wide range of training ranging from chemical risks to plastic welding techniques.